Stofix
Case Study
Established in 1993, Stofix design and manufacture the industry’s most innovative brick slip solution.
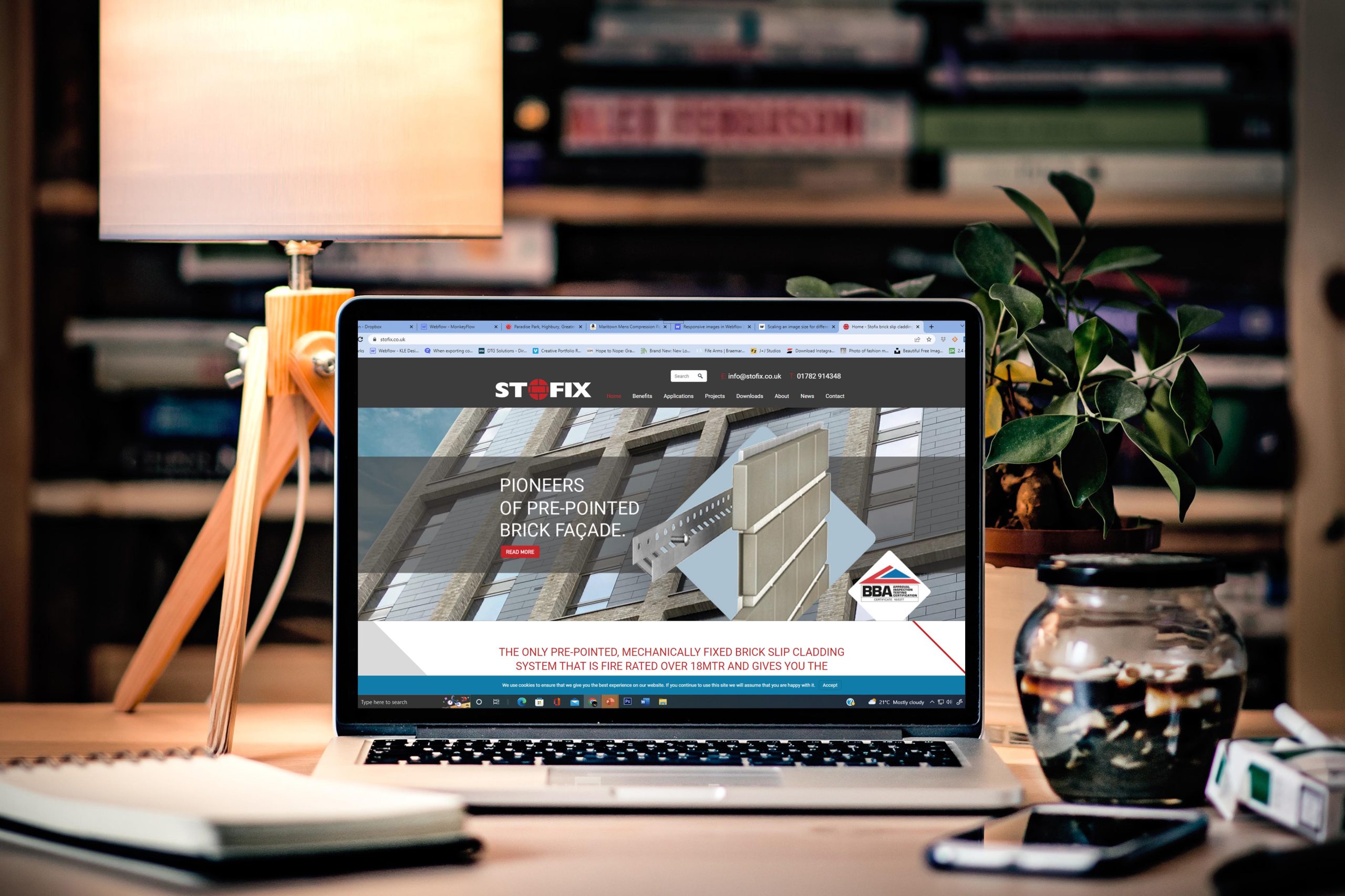
Introduction
Stofix design and manufacture an innovative brick slip cladding system and since forming in 1993 have built a strong presence in the UK and across Europe.
Continuously developing and refining their product has seen them reduce building time and their carbon footprint significantly compared to using traditional brick methods.
Problem
The production drawing process was cumbersome and time consuming, issues experienced by all the Stofix design offices.
Once external façade schemes were received from the Architect, Stofix panel types and configurations needed to be designed for suitability and manufacture. This was extremely time-consuming given the near infinite number of panel sizes, edge conditions and brick bonds, it also made creating a predefined CAD library near impossible.
Codes need to be applied to individual panels that reflect their type, size, bond and edge conditions – this was a manual and tedious process that had a high risk of error. Make sheets and schedules would then be created from the codes within the CAD data and sent to the factory.
Given the codes in drawings informed all data sent for production, any mistakes would have a direct impact on what was manufactured by the factory and then sent to site – unfortunately, this was commonplace.
Office wide drawing standards seemed to be lacking as there were inconsistencies in layers, fonts and line weights of issued data.
Solution
The immediate problem to resolve was how to create flexible panel blocks and generate codes programmatically. Achieving this would ensure that the make sheets and schedules would be informed by accurate drawing content thus omitting errors for the factory and site.
This was accomplished by creating a series of parametric panels that could be adjusted to standard sizes and edge conditions, then having each panel code update based on these parameters using custom lisp programming.
Additional custom tools were created that automatically extract each panel onto a make sheet and another that prints a PDF of each one. An Excel extraction tool was also produced that populates a panel schedule with the necessary data required by the factory for manufacture.
MonkeyFlow then adapted their AutoCAD CADflow ribbon plugin to build a bespoke solution for Stofix.
A tab was added containing a series of warehouse files for quick access to the new panels, fixings and additional items commonly required for Stofix drawings. Also included were additional buttons that activated the new custom tools, and the annotation tab that provides all text and symbols.
Roll out was quick and a shared Dropbox folder was created so system updates could be made instantly. A presentation was given to staff members to update them on the new processes.
Result
The impact of the new system was apparent immediately with two significant benefits – a drastic reduction in errors and an equally notable difference in drawing production time.
‘There is now a huge decrease in the errors contained on drawings, it is monitored on KPI graphs. The system completely negates the problem of incorrect block names, which then ensures all data sent to the factory is correct’ commented Craig Nottage, Senior Design Manager.
‘Site is also benefiting – no incorrect panels delivered, and quantities are correct, it’s easier to locate panels and instal on site’.
‘What would traditionally take a user about 4 days to draw a set of elevations, can now be done in 1 day – there’s a massive difference in speed, I can’t stress how much of a difference it makes‘ explained Craig.
Much of the monotonous and tedious tasks such as creating, and printing make sheets have now also been eliminated.
In addition, there has been a ‘definite improvement in the graphic consistency of the drawings, they now look like they have been created by the same office’ added Craig.
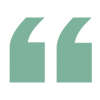
It’s absolutely spectacular, it does exactly what we discussed
Andy McKechnie
Technical Director
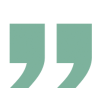
Conclusion
Stofix have now significantly sped up their design program, manufacturing, and site installation.
‘The factory is now insisting all other Stofix design offices use the same the system as it mitigates errors and queries’ commented Craig.